The injection molding process of plastic parts mainly includes four stages: filling - holding pressure - cooling - demolding. These four stages directly determine the moulding quality of the product, and these four stages are a complete continuous process. 1. Filling stage
The filling is the first step in the entire injection molding cycle. The time starts from the time the mould is closed and the injection is started until the mould cavity is filled to about 95%. In theory, the shorter the filling time, the higher the moulding efficiency, but in practice, the moulding time or injection speed is subject to many conditions.
2. Holding pressure stage
The function of the holding pressure stage is to continuously apply pressure, compact the melt, increase the density of the plastic (densification), and compensate for the shrinkage of the plastic. During the holding pressure process, the back pressure is high because the mold cavity is already filled with plastic. During the holding pressure compaction process, the screw of the injection molding machine can only move forward slowly and slightly, and the flow speed of the plastic is also relatively slow. The flow at this time is called holding pressure flow.
3. Cooling stage
In injection molding, the design of the cooling system is very important. This is because only when the molded plastic products are cooled and solidified to a certain rigidity can they avoid deformation due to external forces after demolding. Since the cooling time accounts for about 70% to 80% of the entire molding cycle, a well-designed cooling system can greatly shorten the molding time, improve injection molding productivity, and reduce costs.
4. Demolding stage
Demolding is the last step in an injection molding cycle. Although the product has been cold-formed, demolding still has a significant impact on the quality of the product. Improper demolding methods may cause uneven force on the product during demolding, deformation of the product during ejection, and other defects. There are two main ways of demolding: ejector demolding and stripper demolding. When designing a mold, choose the appropriate demolding method based on the structural characteristics of the product to ensure product quality.
Our factory has always focused on quality management. We have passed ISO9001 certification. On the premise of ensuring the quality of moulds, we pay great attention to the quality of customers' injection moulding products. We have more than 15 years of experience in precision industries such as medical Injection Moulding, automotive molds and Aviation plastic mold.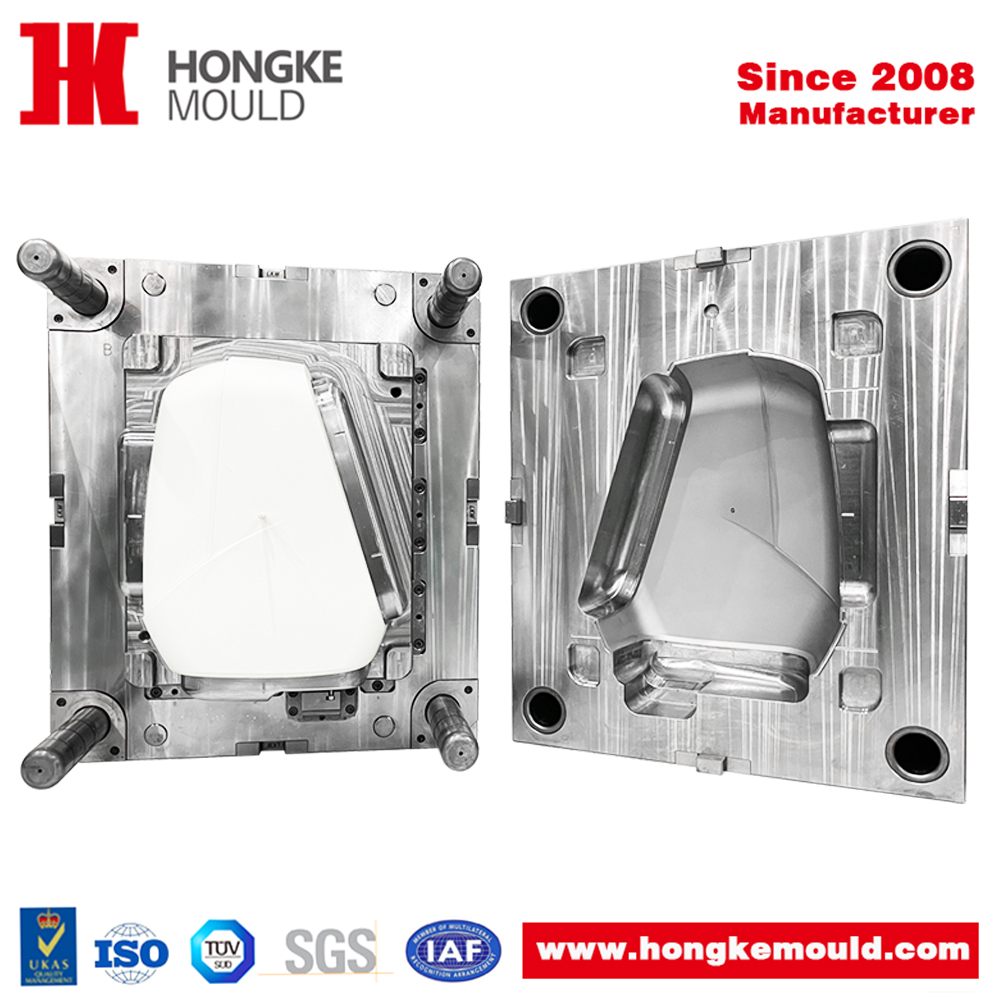